Case Study: High-Performance Workstation Fits Machine-Vision Applications in Semiconductor Manufacturing
Semiconductor manufacturing is an extremely
complex process. It’s been that way since the first wafers rolled off the line but is getting far more complex with every generation of devices.
Factors that contribute to that complexity include:
・Increasing levels of miniaturization and precision, now measured in nanometers.
・The increasing need for cleanroom environments.
・The multi-step processes required for semiconductor manufacturing, such as photolithography, etching, deposition, and diffusion.
・Advanced materials in use, beyond the traditional silicon.
・The quality control and testing procedures that come into play, as well as the need for increased security.
Related to each of these complexities, semiconductor manufacturing is now facing a series of challenges including utilizing new materials to develop a smaller die with higher performance and reduced power, a continually change in manufacturing requirements, and a post-COVID supply chain in flux, making it difficult to obtain materials.
Keeping Costs in Check
Cost pressures continue to be a burden for semiconductor manufacturers. Having up to date manufacturing equipment is obviously necessary, but also comes at a steep cost. Moving to smaller nodes (smaller physical sizes) is a requirement to remain competitive. Leading-edge manufacturers are producing die at 7nm and 5 nm, with smaller geometries being explored.
Unfortunately, as transistor sizes shrink, the power density on the semiconductor die increases. Effectively managing heat generated by densely packed transistors is critical to prevent thermal issues that can affect device performance and reliability. The bottom line is that it’s imperative to keep yields at or above acceptable levels, regardless of the technologies and geometries.
There’s also a need to “do more with less,” whether it’s personnel, materials, and/or time. It’s no secret that there’s a talent shortage in the high-tech arena, and any process that can be automated, whether partially or completely, is welcome.
Machine Vision Brings Needed Assistance
One technology that can play a crucial role in bettering semiconductor manufacturing is machine vision. If implemented properly, machine vision can simultaneously provide automated inspection, quality control, and process optimization. It can provide these benefits in a variety of ways, including defect detection and classification, where the machine-vision systems help inspect semiconductor wafers and chips for defects. High-resolution cameras would be employed to capture images, and advanced algorithms analyze the images to quickly and accurately detect and classify defects.
Employing machine vision in semiconductor manufacturing holds a host of benefits, ranging from higher quality products to reduced overall costs.
Further along in the manufacturing process, the machine-vision systems can inspect entire wafers and individual die for defects and inconsistencies. This process is known as automated optical inspection, or AOI, and it was previously handled manually by human eyes at a far slower speed, and less than stellar results.
In addition, machine-vision systems can capture and store visual data throughout the manufacturing process providing a detailed record of each step. This traceability is valuable for quality control, troubleshooting, and meeting regulatory requirements. Then, by connecting the machine-vision system to other components within the network, like artificial intelligence (AI) and the industrial IoT (IIoT), even further gains can be realized. Other functions the system could perform include hardware positioning, material and component identification, verification, and an array of measurements.
In a typical configuration, the machine-vision system for semiconductor manufacturing typically consists of several key components working cohesively to capture, process, and analyze visual data. The specific components would likely include high-resolution cameras, a consist lighting/illumination system, conventional 2D and 3D sensors, a frame grabber, an image processor, a communications interface, storage, and a base computing platform.
This final component is the brains/backbone of the machine-vision system, and it is equipped with all the necessary software, running in real time. All data passes through this central point and is directed to the proper entity. The base platform would also integrate the machine-learning and predictive maintenance techniques that can be beneficial to the end application. It’s also this central component that determines if, when, and how an administrator should be alerted.
One vendor that stands out in this application area is Vecow, who offers a diverse range of products that cater to these semiconductor-manufacturing needs. The company excels in system integration, ensuring seamless compatibility with existing systems. With extensive experience in machine vision, Vecow allows its customers to deliver high-accuracy solutions for efficient inspection in quality-control processes.
Real-time inspection is a burgeoning area, and it takes a high-end platform to handle all its intricacies.
Vecow RCX-3000 PEG Workstation
Vecow is committed to ensuring compatibility and facilitating smooth integration into potentially diverse environments. With its long-term supply capabilities, customers are ensured continuity, reliability, and a stable source of computer hardware. The company’s RCX-3000 PEG workstation is designed with both an Intel CPU and an NVIDIA-based graphics card. Such horsepower makes it a great candidate for machine-vision systems for semiconductor manufacturing. That level of processing also permits fast 3D processing and deep-learning AI from high-speed 3D cameras and associated software.
Vecow developed the RCX-3000 PEG workstation-grade industrial PC (IPC) with machine vision system integration customers in mind. Specifically, the system can be equipped with a high-performance Intel Core i9/i7 processor and NVIDIA’s GeForce RTX 40 series graphics cards. The maximum power budget is more than ample, with a maximum of 1800 W. The flexible input power design operates from 16 to 50 Vdc or 220 Vac.
PCIe expansion is handled through up to seven expansion slots, with PCIe 4.0 x16/PCIe4.0 x8 and PCIe x4 signals for the NVIDIA graphic cards, and USB/10G/PoE+ expansion cards for the cameras, four DisplayPort connections for 4K resolution. A USB 3.2 Gen 2x2 Type C offers a maximum speed of 20 Gbits/s, maximizing flexibility.
While the RCX-3000 PEG is well suited for the described machine-vision in semiconductor manufacturing, it can also operate as the workhorse in related applications. Those could include autonomous mobile robots (AMRs), deep learning, and/or vehicle computing.
Vecow’s RCX-3000 PEG workstation is well suited for machine-vision applications in semiconductor manufacturing. Based on Intel CPUs and NVIDIA graphics cards, it can handle just about any application related to machine-vision.
As a respected global supplier, Vecow has demonstrated its expertise in machine vision applications through a number of existing partnerships. To learn more about this blossoming field, or the related applications discussed here, contact the company at
[email protected].
Related Products
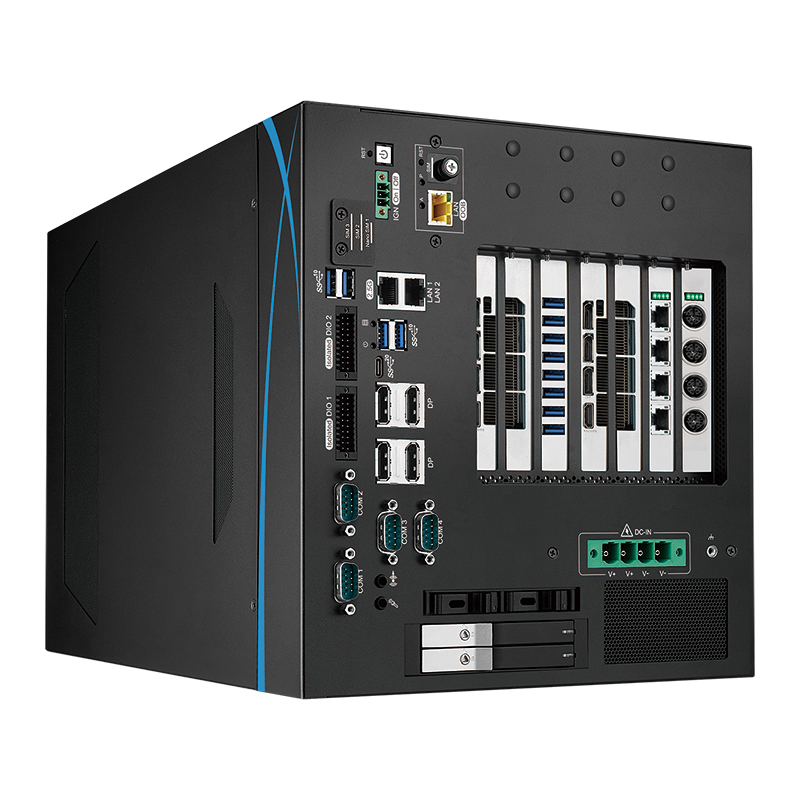 |
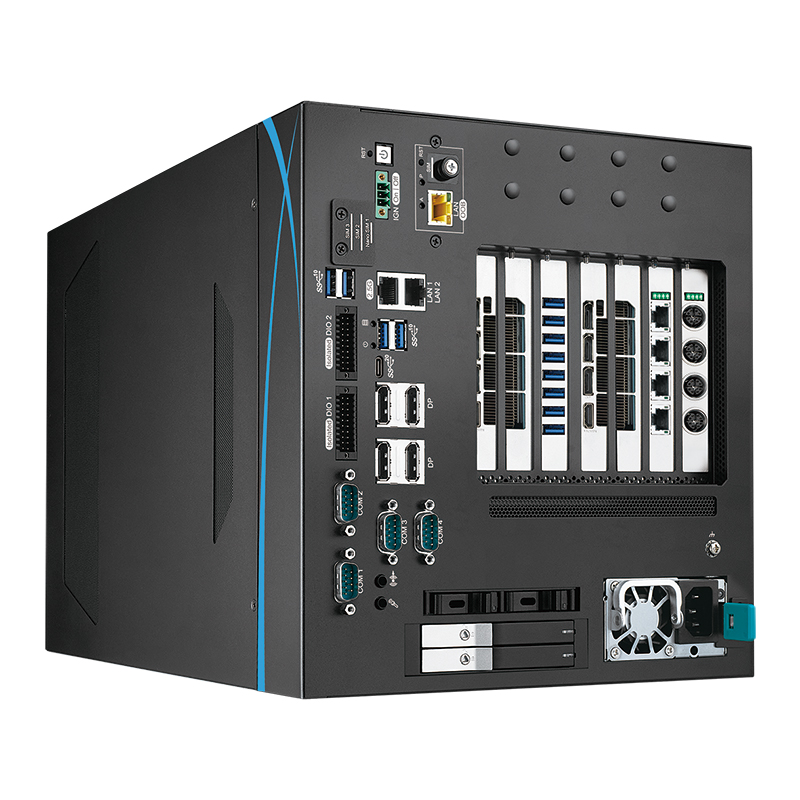 |
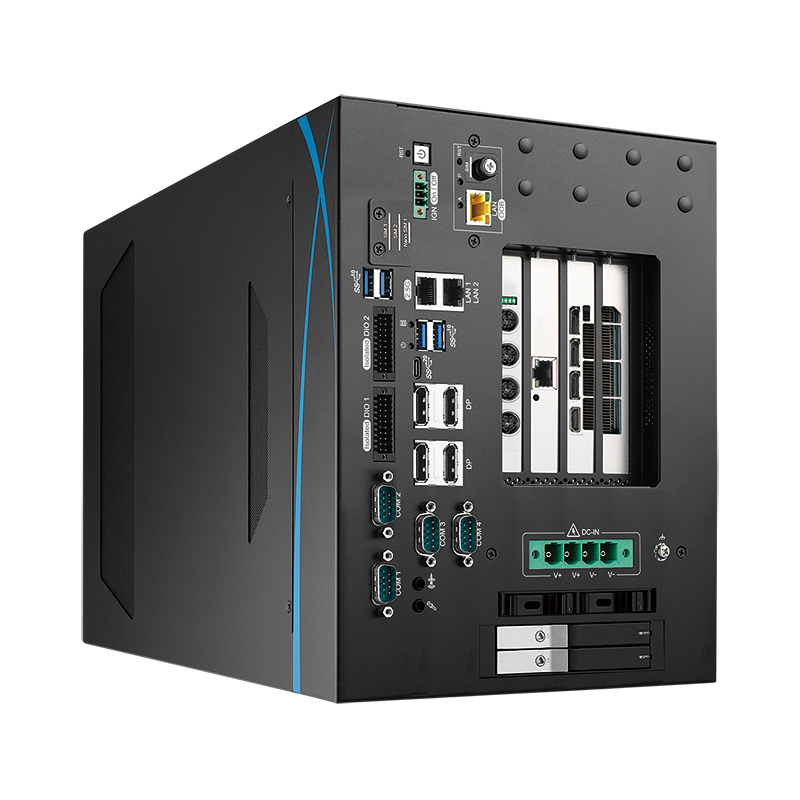 |
RCX-3750 PEG
Intel® Core™ i9/i7/i5/i3, 1800W PEG, 2.5G LAN, 5 PCIe Slot, DC Power, SW Ignition, vPro
|
RCX-3750A PEG
Intel® Core™ i9/i7/i5/i3, 1800W PEG, 2.5G LAN, 5 PCIe Slot, AC Power, SW Ignition, vPro
|
RCX-3430 PEG
Intel® Core™ i9/i7/i5/i3, 1800W PEG, 2.5G LAN, 4 PCIe Slot, DC Power, SW Ignition, vPro
|
Related Solutions